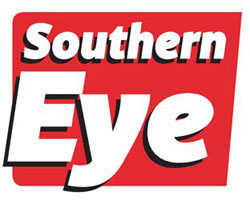
LOCAL production of titanium metals is still a long way off, though encouraging progress had been made in developing a suitable technology, MPs heard on Tuesday.
South Africa has the world’s second-largest reserves of titanium — an extra-strong, corrosion-resistant metal that is used in aircraft, ships and medical implants — but currently exports the raw material for beneficiation elsewhere.
“Considering the value chain of titanium, SA is currently at the bottom of the chain, mining and exporting the mineral as titanium-bearing slag while all titanium metal has to be imported at high cost to the country. This is considered to be a market failure,” Bloemfontein’s Central University of Technology’s Willie du Preez told Parliament’s trade and industry committee on Wednesday.
The briefing on titanium formed part of the committee’s colloquium on beneficiation. Titanium oxide is found in ilmenite deposits in Namakwa Sands on the Western Cape coast and in the sands of Richards Bay, where it is mined by Tronox and Richards Bay Minerals respectively.
Du Preez said titanium slag sold for about $1,45/kg and a titanium ingot cost about $20/kg.
He said if a pilot project to produce titanium powder from titanium petrochloride, which was being conducted by the Council for Scientific and Industrial Research, was successful, a feasibility study costing about R80m and funded by the Industrial Development Corporation (IDC) and Tronox would be undertaken, possibly next year.
If the study was successful, a 500-tonne-a-year demonstration plant would be built, followed by a manufacturing plant producing about 20 000 tonnes of titanium a year.
“People are excited about the progress,” du Preez said, though he noted that if each stage was successful, the construction of a manufacturing plant was only likely in about 2020 to 2022.
- Chamisa under fire over US$120K donation
- Mavhunga puts DeMbare into Chibuku quarterfinals
- Pension funds bet on Cabora Bassa oilfields
- Councils defy govt fire tender directive
Keep Reading
“The development and commercialisation of beneficiation processes do not happen overnight – perseverance is required, especially when unforeseen stumbling blocks or delays are encountered.”
For example, it took about 20 years before Sasol was in a position to produce synthetic petrol from coal.
Du Preez said it was crucial that funding for research and development, which had cost about R250m so far, was sustained.
The Department of Trade and Industry has targeted development of a local titanium manufacturing capability in the latest version of its industrial policy action plan. An interdepartmental titanium task team has been formed with representatives from the departments of science and technology, trade and industry, mineral resources, and public enterprises, and from the IDC.
Du Preez told the committee government recommendations on the local manufacture of titanium and titanium oxide products dated back to 1999, but it was only in 2009 that a Titanium Centre of Competence was established to co-ordinate research and development as well as commercialisation of the product.
This was stimulated by the interest of major aerospace players Boeing and Airbus and the growth of local demand for the product.
He said the centre was developing a number of technology platforms essential for production of a range of products, but had to be industrialised and commercialised. At any point there were 80 researchers and 20 postgraduate students in SA who were involved in developing the technology building blocks for a local titanium industry.
African National Congress expert on beneficiation Ben Turok bemoaned the slow progress and said that in technological innovation, risks had to be taken.
— Online