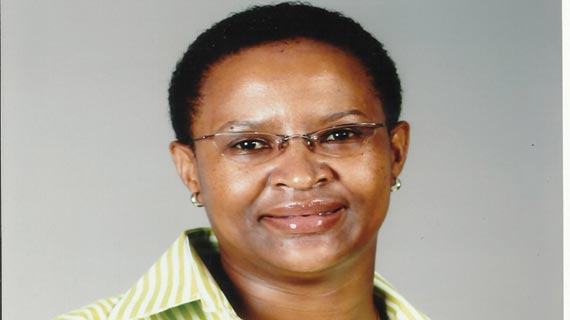
Total quality management just like the marketing function of an organisation is the responsibility of every member of the organisation.
Naturally it is easier for the marketers as they are involved with the customers much more because it is their duty to correctly identify customers’ needs. Once they have identified the customers’ needs they have to explain these needs well to designers who then make the product.
It is also the responsibility of marketers to train the customers on product use and to ensure that the customers are always satisfied with the product and secure repeat business. Having said this, the production line cannot produce a sub-standard product and get away with it because they are not in direct contact with the customers.
Obviously a defective product is in essence a waste of raw materials and would come hard on the production team just as it would to marketers and to accountants.
Total quality management techniques must involve the whole chain because the bottom line affects the whole chain. Whether the product is finally sold, or not sold, for that matter impacts financially on the whole chain which is out to make a profit while satisfying the customer.
It is important for everyone in the chain to understand that product and/or service quality, customer satisfaction and company profitability are intimately connected.
It would also be important to ensure that there are zero defects in the whole supply chain as the emphasis would be on process rather than output. A quality product is only achieved if all the parts to the whole are made with utmost care.
Supply chains that have cut corners in an effort to lower costs have paid the price when the quality of the customer’s experience suffers. The supply chain as a whole must seek prevention rather than later detection of defects.
- Chamisa under fire over US$120K donation
- Mavhunga puts DeMbare into Chibuku quarterfinals
- Pension funds bet on Cabora Bassa oilfields
- Councils defy govt fire tender directive
Keep Reading
Total quality is everyone’s job in the supply chain as it follows that it is everyone’s job to satisfy the customer. Both the systems and the management in the supply chain should be finely tuned for continuous improvement and total quality.
To achieve total quality in the supply chain, each link must identify internal supply chain customers and establish communication linkages. All members in the supply chain must conduct regular performance reviews. The same high standard of commitment is required at each stage so that there is a smooth flow right up to the end of production.
Every link has to be on time all the time.
A defect-free product or service is the reflection of the high standard that was practiced at each step of the way where the smaller components were made and then joined together to come up with the total product.
It must start with the cleaner who realises that the components need to be manufactured under a clean, healthy environment to allow the producers to produce the components in comfort right up to the final sales that may involve the gatekeepers and all the other staff in the organisation who should understand that the customer is king.
When an organisation is serious about total quality management, it is contributing immensely to company profitability which is the whole reason why businesses are set up. Until next week, remain Brand Savvy!